Advanced Thermal Waste Water Treatment
- AIChE-VIT
- Dec 28, 2022
- 3 min read
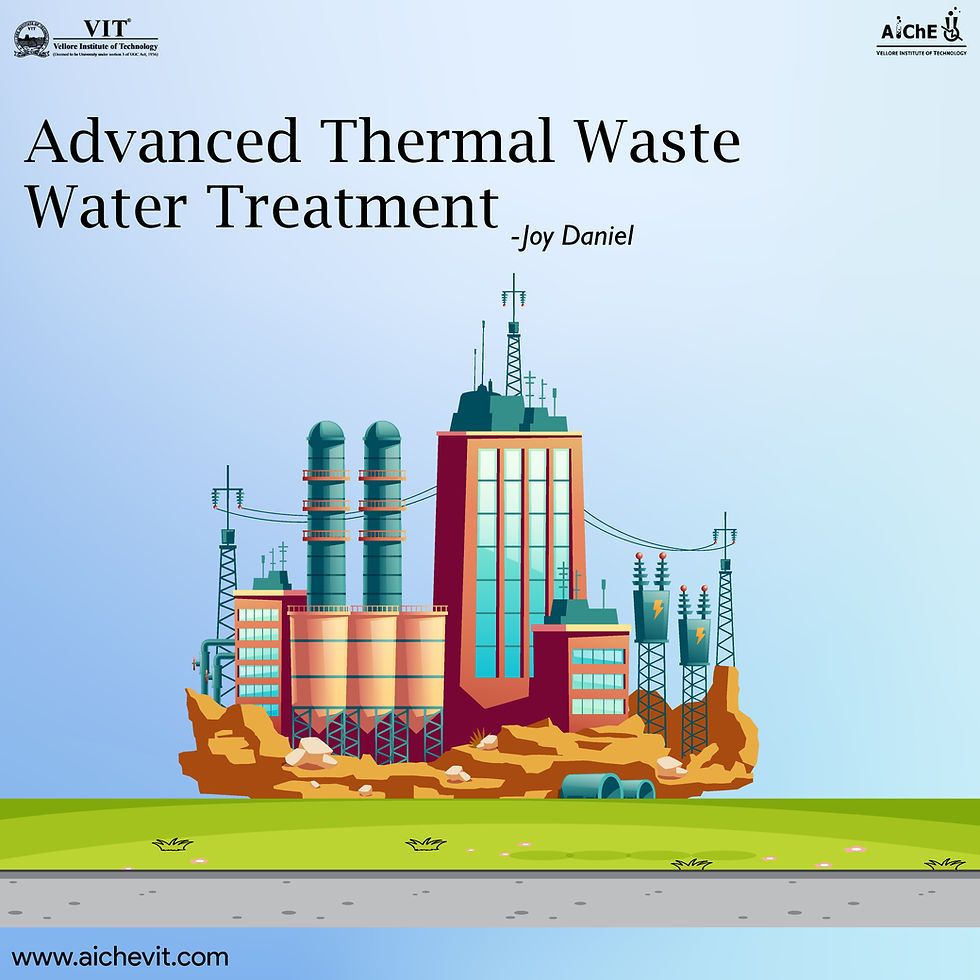
Ever wondered where all the wastewater we produce domestically and industrially on an everyday basis is taken? What happens to it? How is it treated? Where is it discharged? If not, then allow me to explain. Wastewater in general is the ‘by-product’ that is formed after using fresh water in various applications like leaching, flushing, industrial treatment etc. This wastewater is amassed from domestic waste, industrial waste, and other wastes, which is then sent to big factories, where it is treated at Sewage Treatment Plants. Here, it is first treated by conventional methods, which are a combination of physical, chemical, and biological processes consisting of procedures to remove solids, organic matter, and sometimes, nutrients from wastewater. After this, the partially treated effluent (liquid waste) is taken and is used either for irrigation purposes or discharged into inland waters, estuaries, and the sea.
However, that is not where things end when we specifically take industrial wastewater under scrutiny. Conventional treatment methods are not the best options for knocking out the high organic load (BOD, COD) present in the effluent. Even after an extensive-conventional treatment, the industrial effluent contains toxic constituents like heavy metals (chromium, cadmium, arsenic, nickel) and polycyclic aromatic hydrocarbons. And that is where the recent advanced technology for effluent treatment comes in. This technology has enabled us to remove toxic and unwanted substances, reduce high TDS content (Total Dissolved Solids), high organic load and even separate the pollutant-free wastewater for irrigation purposes. The advanced technology that has aided in treating the bio-recalcitrant contaminants includes thermal treatment units called Steam Strippers, Multiple Effect Evaporators (MEE) and Agitated Thin Film Evaporators (ATFD).
As the name suggests, a ‘steam stripper’ uses steam to strip off and separate volatile liquids from a solution. The stripping is based on their boiling point and is done in the solution under negative pressure. As the influent is evenly spread and comes in contact with steam, the more volatile liquid (one with the lower boiling point) vapourises and is expelled along with the steam. The hot vapour is then channelled through a condenser and converted back into liquid without the waste. When the pressure decreases, so does the boiling point, hence enhancing the efficiency of the process.
In the case of MEE, wastewater is boiled in a sequence of vessels, each held at a lower pressure than the last. Because the boiling temperature of water decreases as pressure decreases, the vapour boiled off in one vessel can be used to heat the next vessels successively, thus saving energy and overall operational costs. Only the first vessel (one at the highest pressure) requires an external source of heat to kick-start the course of action. The vapour coming out from each vessel is condensed and later used in industries as recycled water.
The concentrated sludge that is left in the MEE, after stripping of its remaining water, is passed through an ATFD (Agitated thin film drier), which converts this concentrated slurry from MEE to powder or flakes. The powder mainly contains sodium and mineral salts, which can also be of industrial use. MEE is widely used for product concentration and has now been used for the recovery of water from wastewater which can be reused for industrial operations (as mentioned earlier), thus reducing overall freshwater demand for the industry, leading to zero liquid discharge and sustainable development.
Pharma effluents
Pharmaceutical components, which are frequently detected in natural and wastewater bodies, as well as drinking water, have attracted considerable attention because they do not readily biodegrade and may persist and remain toxic. As a result, pharmaceutical residues pose ongoing and potential health and environmental risks. To tackle these emerging contaminants, Advanced Oxidation Processes (AOPs) such as photo-Fenton, son-lysis, electrochemical oxidation, radiation and ozonation have been applied to remove pharmaceuticals. These processes utilize the high reactivity of hydroxyl radicals to progressively oxidize organic compounds to innocuous products.
A way to use conventional methods in recalcitrant pollutants
In the Pharma industry, while having to deal with the optimum amount of waste produced by it, AOPs(Advanced oxidation processes) have given a further boost to their wastewater treatment by the removal or degradation of toxic organic pollutants. These can also be used as pre-treatment to convert recalcitrant pollutants to biodegradable components and hence be treated by conventional biological methods.
- Joy Daniel
Comments